An Alternative to Mass 3D-Printing
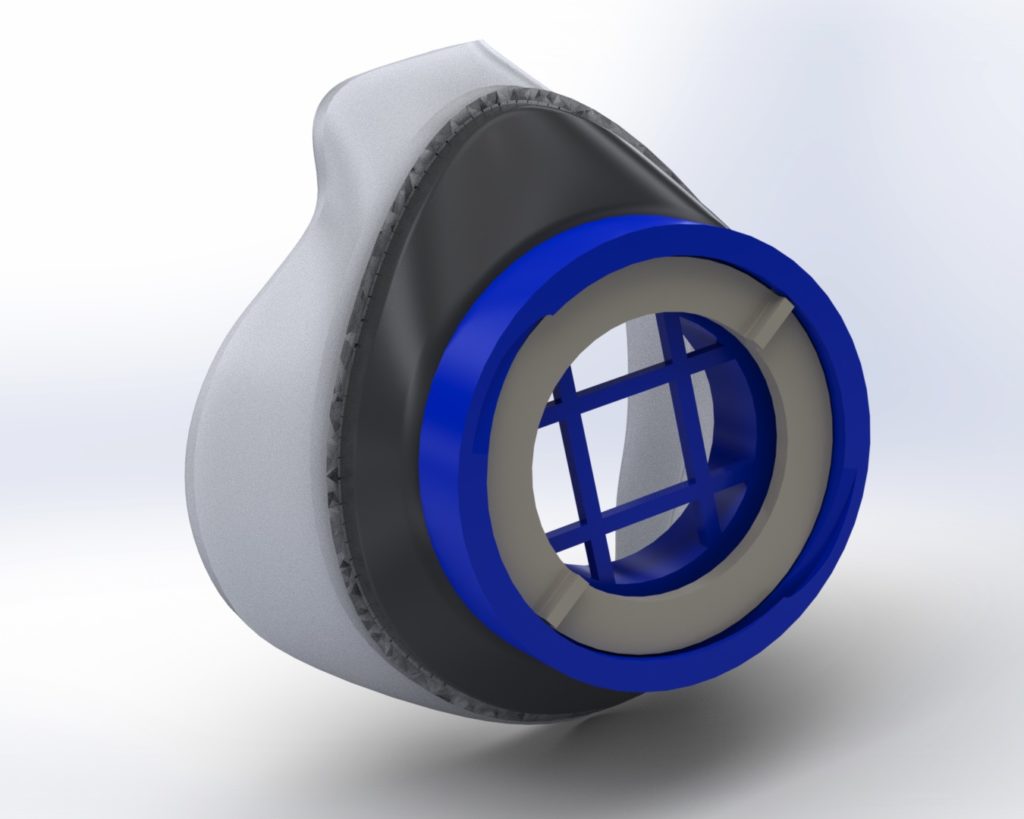
Team Members
Omar Soufan (Technical Associate – Mech. Eng.)
Catherine Krawiec (CMTI Student)
Erin Minervini (CMTI Student)
Martin Gira (Senior Research Engineer – URMC)
R. Scott Russell (Senior Technical Associate – Mech. Eng.)
Mitch Anthamatten (Professor and Chair – Chem. Eng.)
Ibrahim Mohammed (PhD Student – Mech. Eng.)
Madelyn Jeske (PhD Student – Chem. Eng.)
Abstract
In response to the COVID-19 crisis, we are developing a mask that offers superior function in a fraction of the manufacturing time when compared to many emerging 3D printed mask designs. The design offers an improved seal around the face that is more comfortable, a more robust/airtight filter housing, autoclavable materials, and a quicker manufacturing method. This will allow local and national entities looking to produce DIY masks a better, faster alternative to 3D printing.
Pitfalls of 3D Printed Masks
Imperfect seal around the face
The main issue associated with 3D printed masks is gapping that’s created around the face due to the rigidity of the mask. If worn loosely, these gaps present the opportunity for the user to exchange unfiltered air with the environment. If worn tightly to eliminate these gaps, the rigid structure can cause bruising and severe discomfort to users who often have to wear the masks for hours at a time.
Filtering efficacy
Many 3D printed mask designs hold a filter material between two 3D printed grids. These grids frequently friction fit together and will have air space around the filter material. Like the air gaps around the face, this leads to the potential for exchange of unfiltered air between the user and their environment.
Sterilization
The material and geometry inherent to 3D printed parts limit the sterilization methods that can be used to clean them and makes viable methods less effective. Conventional steam sterilization happens between 120-135 degrees Celsius at a pressure of 15 psi. Common 3D thermoplastic printed materials such as PLA, ABS, PETG, and Nylon have heat deflection temperatures of 60 deg C, 98 deg C, 70 deg C, and 110 deg C respectively. Attempting to sterilize these parts with steam would result in severe deformation.
Alternative chemical sterilization methods raise questions about the compatibility of the chosen thermoplastic with the chemical disinfectant. Many disinfectants break down plastics and cause premature mechanical failure. Also, the inherent stepping, anisotropy, and porosity of FDM printing lead to tiny crevices that are breeding grounds for microbes and difficult to access with disinfectants.
A final alternative is to designate the masks as disposable. However, manufacturing time and materials make single-use masks an undesirable option.
Manufacturing Time
Desktop 3D printers are notoriously slow. Even with thoughtful design and slicing of a model, print time for an individual mask is at least 2-8 hours. This lead time necessitates facilities with ‘print farms’ or requires many individuals to produce enough units to meet demand.
Our Design
Our design attempts to address each of the aforementioned problem areas with changes in design and material choice.
Seal around the face: Our design features a silicone cushion around the rigid body of the mask, which is modeled after CPAP masks. When the mask is secured to the user’s face, the cushion creates an air-tight, comfortable seal.
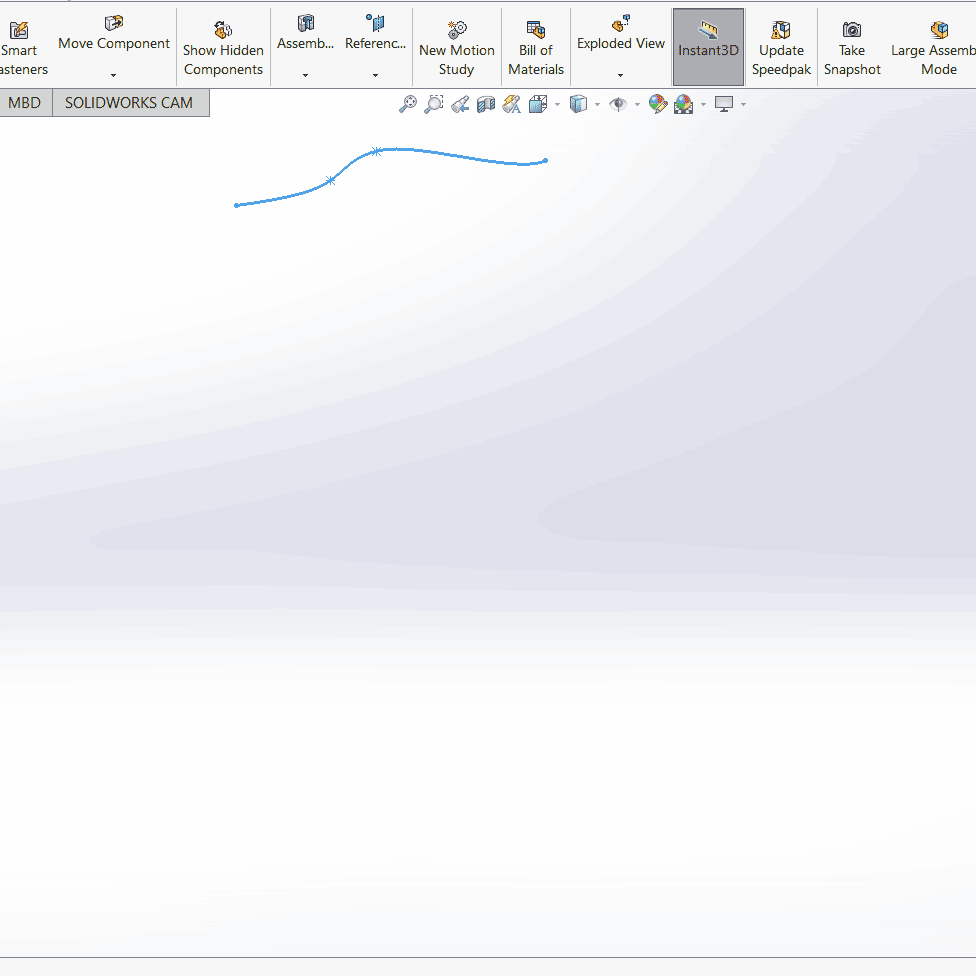
Filter assembly improvement: The filter assembly we’ve designed features locking nuts that tighten O-rings against the filter within the filter housing. This prevents air gaps and ensures that all air that enters/exits the mask has passed through the filter material.
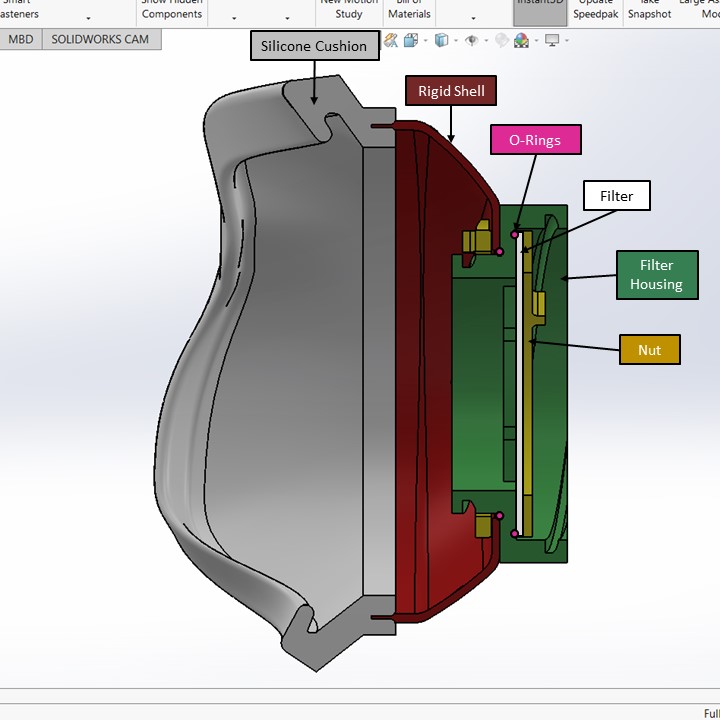
Materials and manufacturing: The cushion is cast into a mold, and is made of a thermoset, skin-safe silicone. For the rigid shell and filter assembly, thermoforming and casting are both being considered. The thermoset materials to be used in casting are highly resistant to heat, making them compatible with steam sterilization. Additionally, casting results in a solid part, compared to the layer lamination of 3D printing. This gives more isotropic material properties and eliminates the issue of stepping and porosity. The materials we’ve selected also have curing times of less than 1.5 hours. With gang molds, tens of these pieces can be cast and cure simultaneously.
In these ways, the materials and manufacturing methods we’ve chosen fit more easily into standard methods of sterilization, are more structurally sound, and the manufacturing time per piece is an order of magnitude less than that of 3D printing.
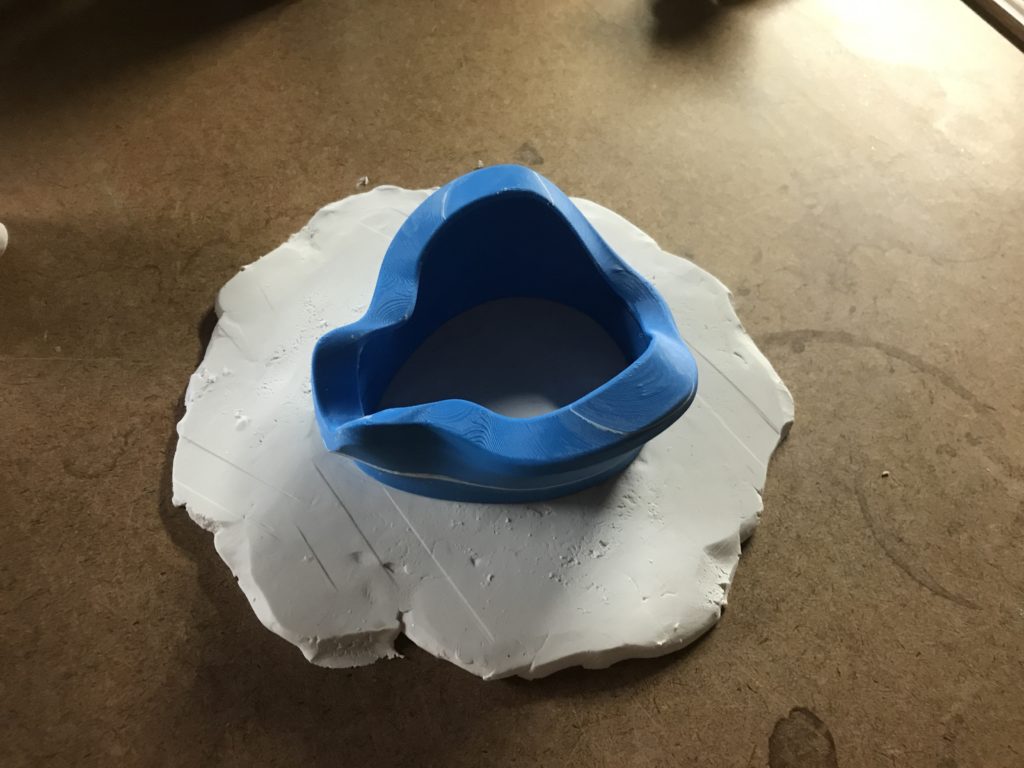
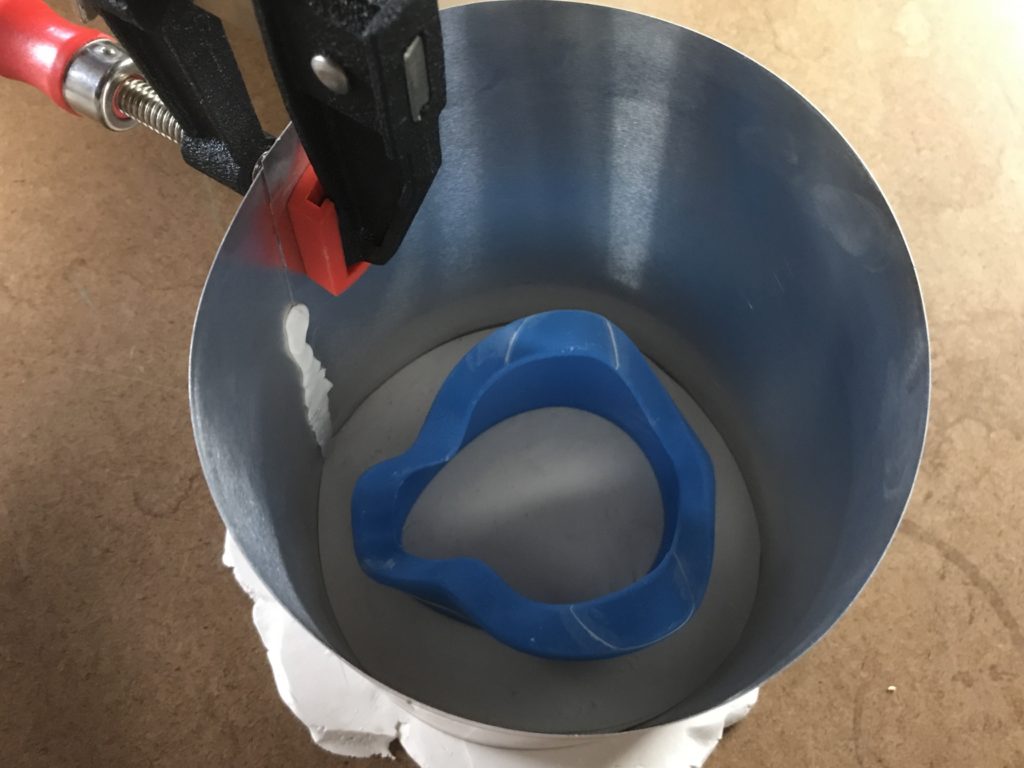
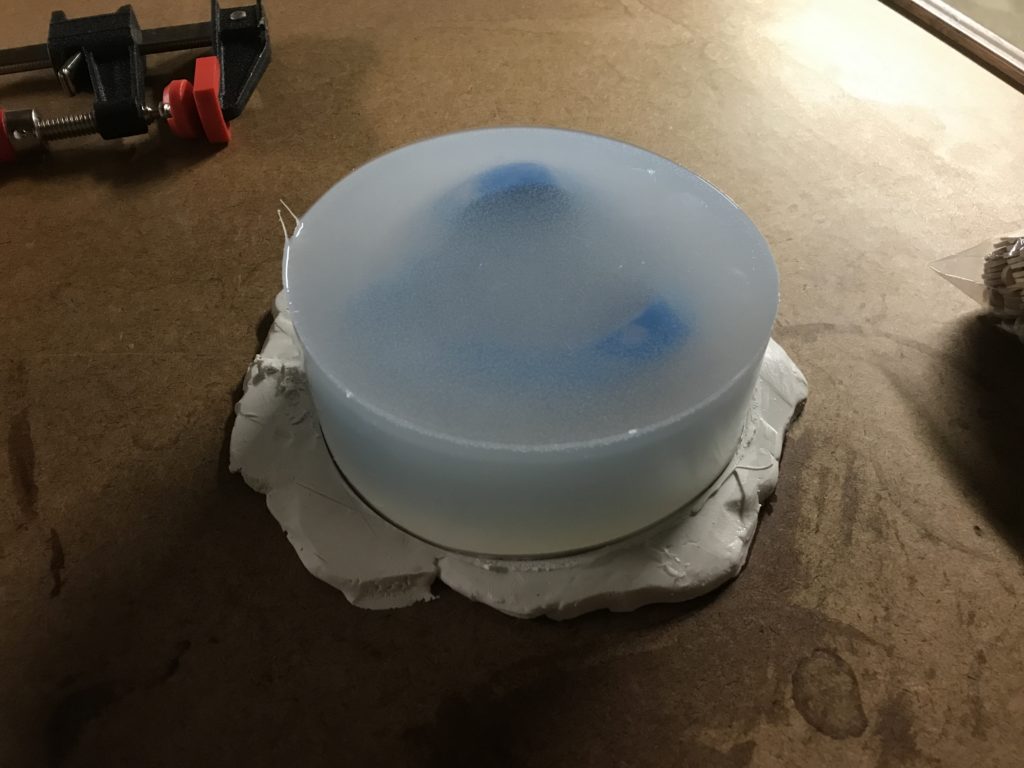

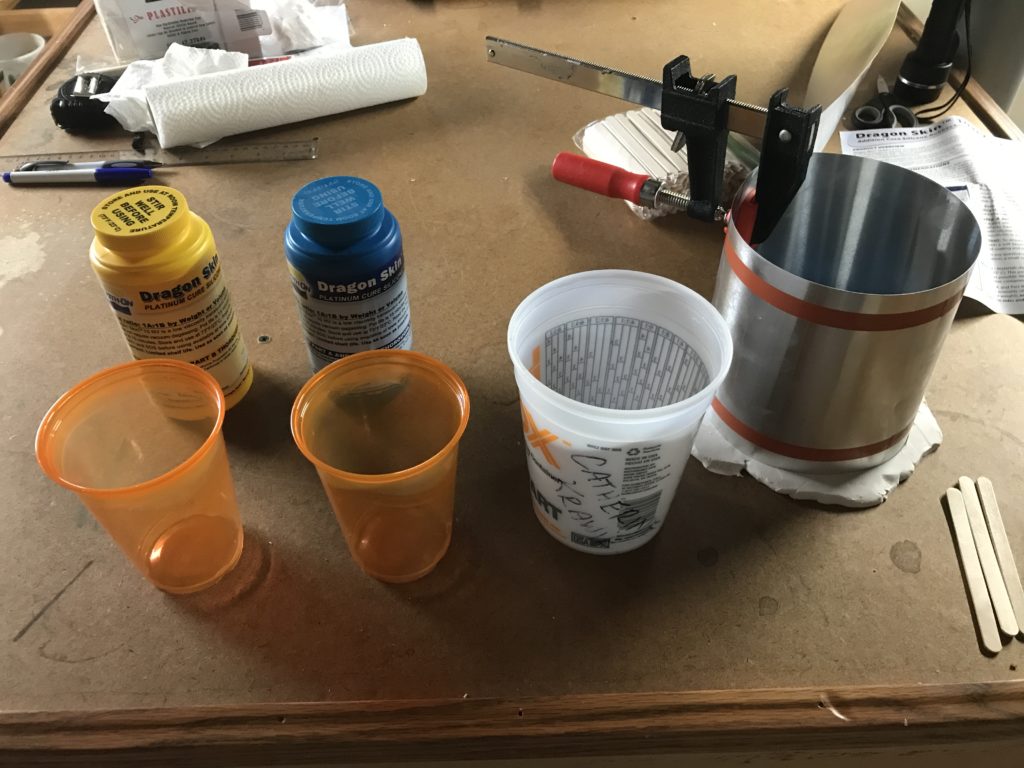
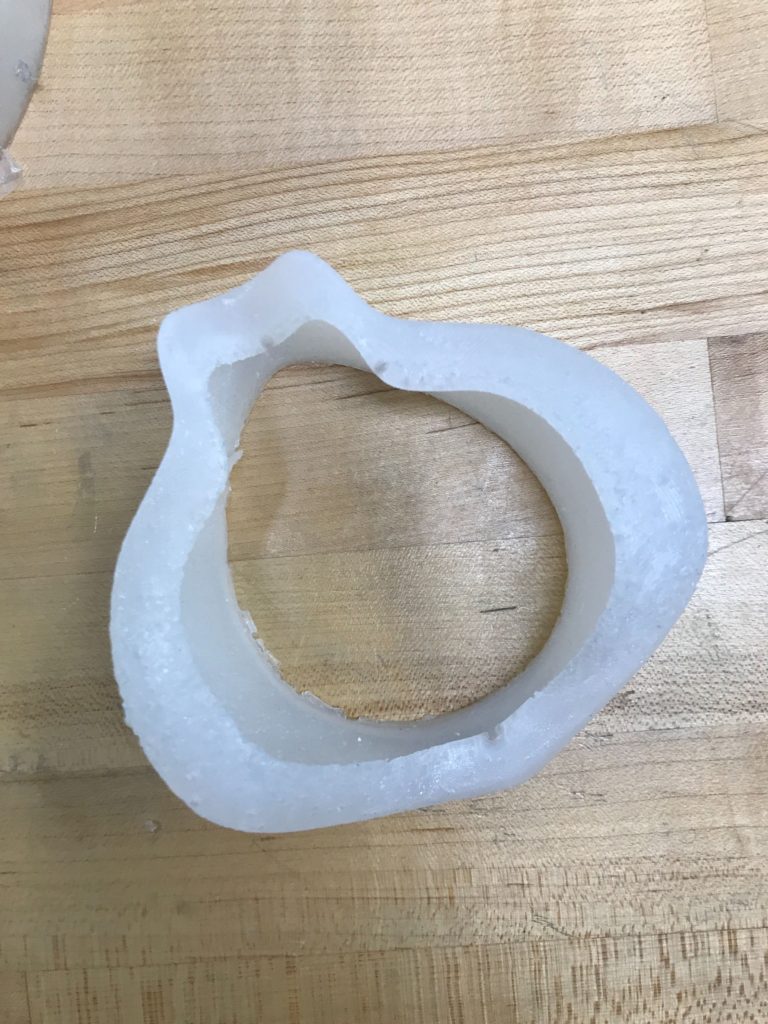
Prototyping progress and future steps
Trial casting and thermoforming is currently being done to refine the design for manufacturability and functionality. Once a minimally viable product is produced, we hope to eventually bring the design to the open-source FDA/NIH 3D Printed PPE file exchange platform to be assessed and approved as ‘Reviewed for Clinical Use’ by the FDA and then distributed to capable manufacturers in areas of need.