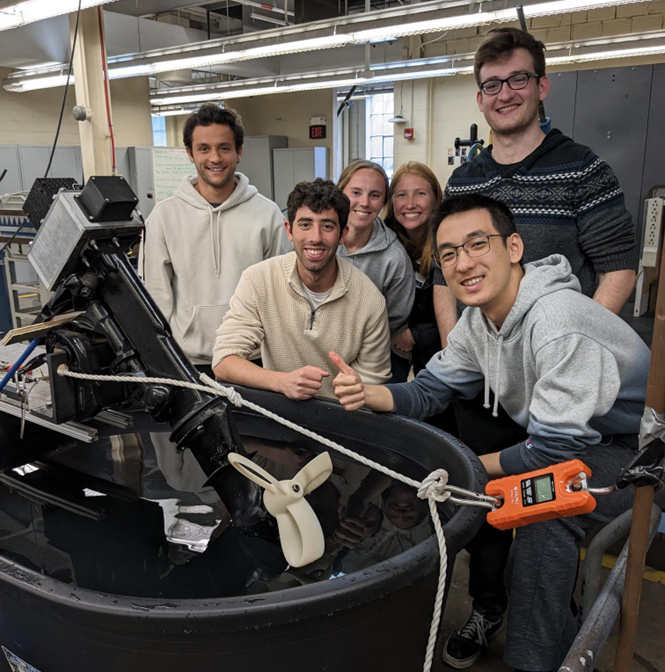
Enhancing Marine Propulsion Efficiency: Design, Simulation, and Testing of a High-Efficiency Toroidal Propeller for Solar Splash Competition
People
Team Members
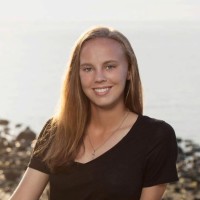
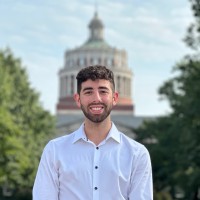
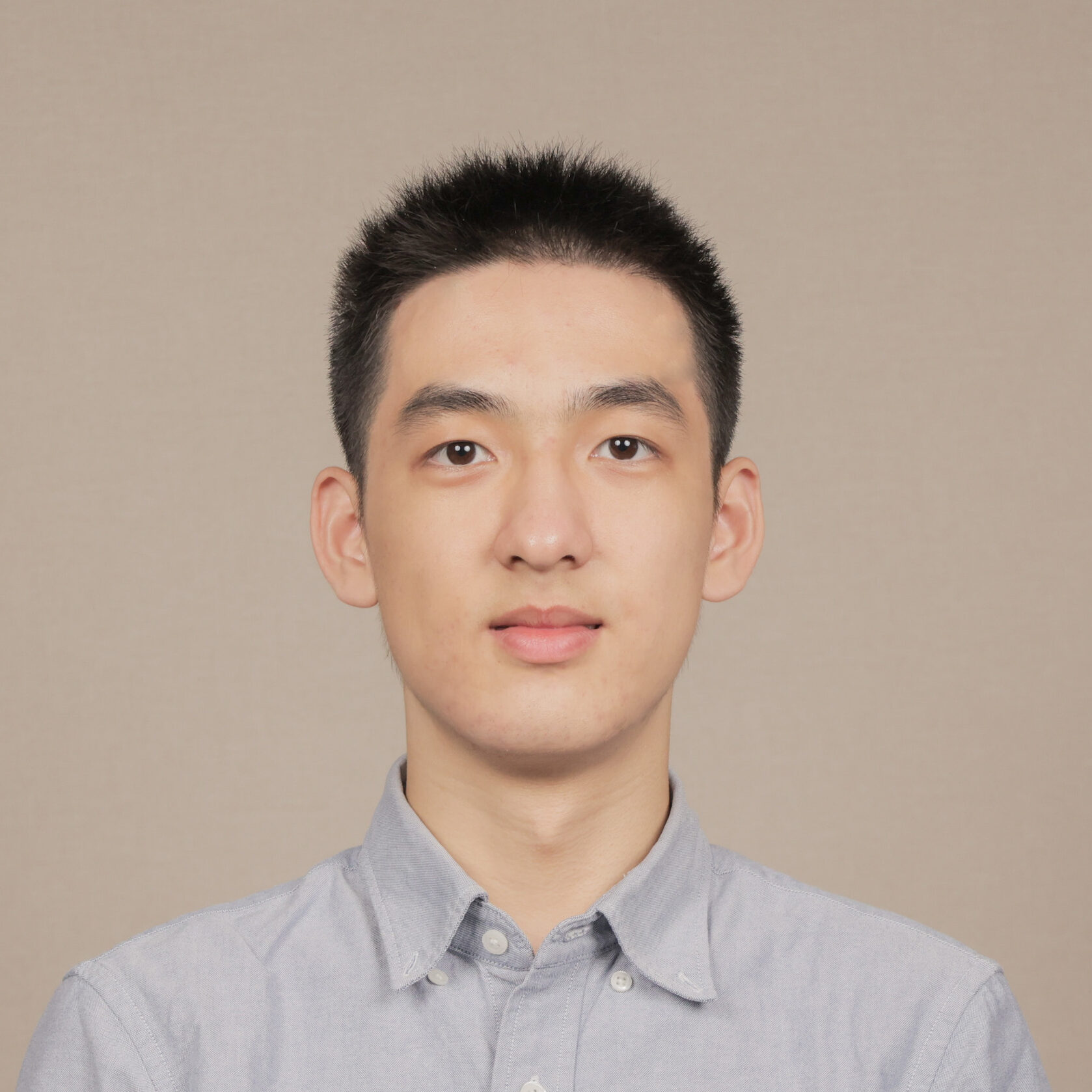

Santino Lupica-Tondo
Role: Tester
Mentor
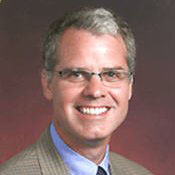
Abstract
Toroidal propellers are at the forefront of marine propulsion innovation due to their increased efficiencies over traditional propellers. This project seeks to capture these benefits and apply them to the University of Rochester Solar Splash Team’s endurance race. A toroidal shaped propeller was designed to improve the open water efficiency of Solar Splash’s current traditional propeller. This would allow the Solar Splash boat to travel a further distance in their endurance race with the same power input. Through testing, simulation, and multiple rounds of optimization, a toroidal propeller was manufactured with a higher open water efficiency as proven through simulation. However, despite the promising simulation results, the propeller did not achieve a higher open water efficiency in testing. This project highlights the challenges of translating simulation results to real-world performance and underscores the importance of rigorous testing in propeller design.
You with me?
Prof. Muir, Fall 2023-Spring 2024
Project Overview
The design journey of our toroidal propeller spans several phases, from initial concept to final testing, reflecting our commitment to rigorous engineering standards and innovative approaches to solving complex problems in marine propulsion.
Problem Definition
The main challenge addressed by our project was the inefficiency of the current propeller used by the UR Solar Splash boat. With the competition date looming on June 4th, 2024, our team was tasked with designing a propeller that could operate more efficiently in open water conditions.
Design Process
The process began with the selection of a toroidal design, motivated by recent advances in marine propulsion technology that suggested increased efficiency and reduced drag. We utilized Siemens NX for the initial designs and StarCCM+ for fluid dynamics simulations to iterate toward an optimal model.
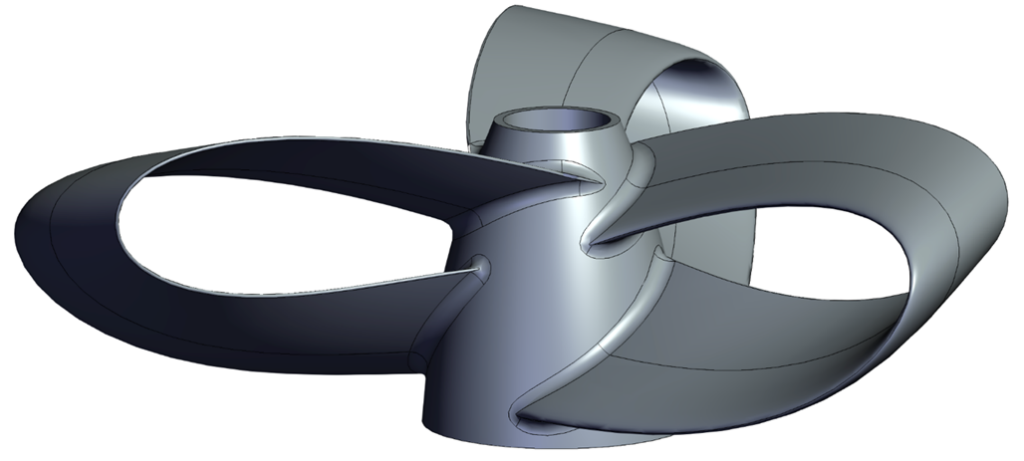
- Simulation: Using Siemens NX and StarCCM+, we simulated various design iterations to predict performance and enhance propeller efficiency.
- Testing: Real-world tests were conducted using a custom-built rig, providing valuable data that helped refine our designs.
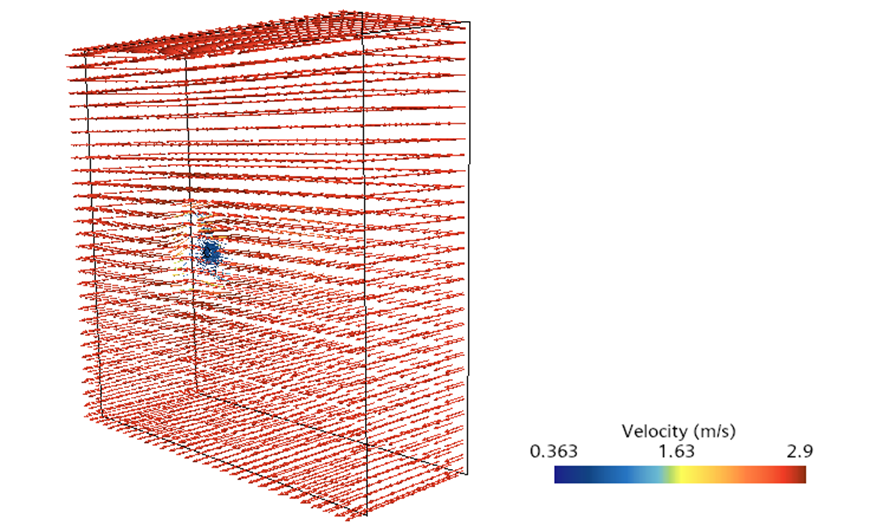
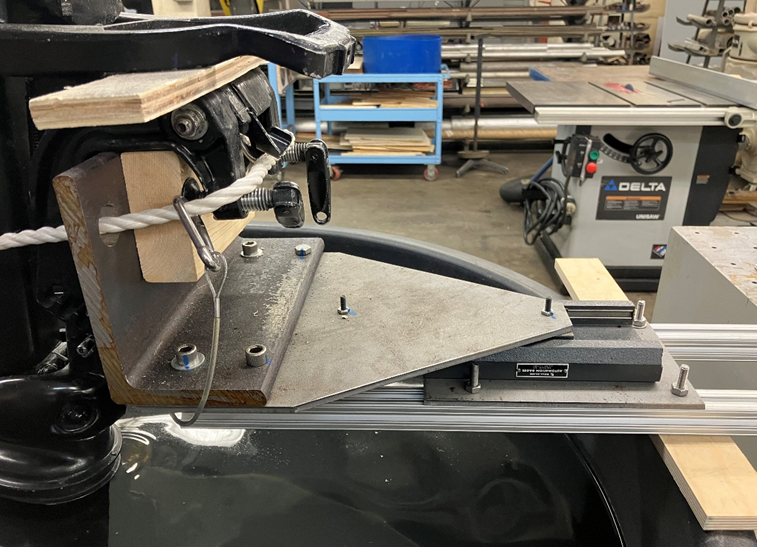
Device Picture
Technical Challenges and Innovations
- Manufacturing the Propeller: Transitioning from 3D-printed models to durable aluminum prototypes posed significant manufacturing challenges, including the need for precise CNC machining to maintain the integrity of the design specifications.
- Material Considerations: The choice of materials was critical, with aluminum offering the best blend of lightweight properties and durability essential for the harsh aquatic environment.
Project Result
Our testing revealed that while simulations suggested significant improvements in efficiency, real-world results were more varied. This discrepancy highlighted the challenges of translating theoretical models into practical applications but also provided a rich learning experience.
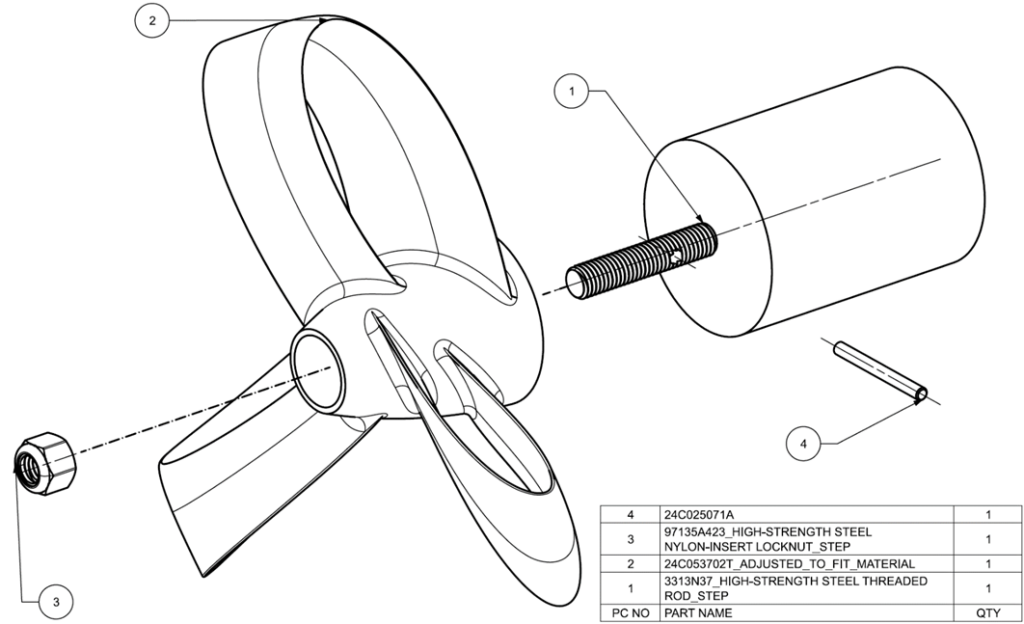
Final Design Report
Presentation Video
Acknowledgements
We extend our deepest gratitude to the following individuals for their crucial contributions to our project:
- Chris Pratt for her exceptional efficiency in securing and delivering the testing rig tank and aluminum rod. Her prompt action enabled swift progress, with materials ready by the next day.
- Bill Mildenberger for generously providing his space and tools in Taylor for our experiments, and for his expertise in assembling the aluminum toroidal propeller.
- Jim Alkins for his dedication in 3D printing our propeller models in Rettner, turning our designs into tangible models.
- Professor Mohammad for his invaluable expertise in simulation setup and access to Blue Hive resources. His efforts to secure a one-month extension were crucial, allowing us to refine our designs and conduct thorough testing. His guidance during the testing phase was especially insightful.
- Professor Muir for his unwavering support and guidance. His mentorship in 3D modeling and experimentation has been instrumental to our project’s success.
We are immensely thankful to each of you for your dedication and support, which have been pivotal to our project’s success.