Description
Our goal for the project was to utilize UV light to disinfect water in an existing water system. Research have shown that the most effective wavelength range for UV light to deactivate pathogens are 100 nm – 280 nm range, which is known as UV-C. This range damages cells in order to deactivate pathogens rendering them unable to reproduce ridding the water of pathogens. Our system exploits this property of UV-C to create an extension for an existing water system that can sterilize the water as the water is flowing through the pipe. To achieve this goal, we designed our system such that the UV-C bulb being held in a quartz tube is suspended in an aluminum pipe by utilizing 3D designed O-rings. The tube for the UV-C bulb is made from fused quartz which has a transmittance of about 99% for UV-C, and the outer pipe is made from aluminum which has a reflectance of around 80-85%. Ideally this allow for most of the UV-C light to be transmitted to the water with any additional light being reflected off of the aluminum pipe. To achieve the required UV water treatment dosage intensity of at least 40 (mW*sec/cm2), we control the flow rate of the water with servos fitted on ball valve to ensure that the volume of water flowing through at any point is irradiated properly to deactivate the pathogens.
Materials
- Aluminum Pipe
- UV-C Bulb (100-300 nm range)
- Quartz Sleeve for UV-C Bulb
- Servo (at least 35kg/cm torque)
- Ball valve
- Water Flow Sensor
- Water Height Sensor
- Relay Switch
**Note: In our system, we built a circuit to implement the relay switch, so the relay switch is able to communicate with the Raspberry Pi to create a totally automated system; however, a physical switch will be enough if total automation is not necessary.
Hardware Implementation
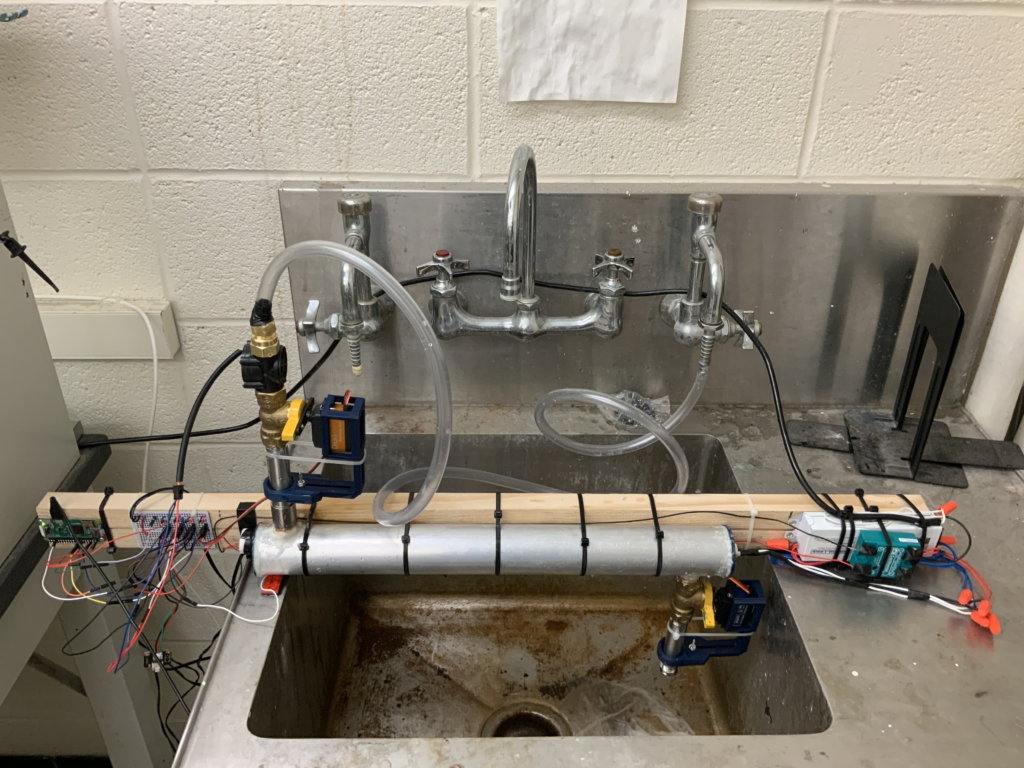
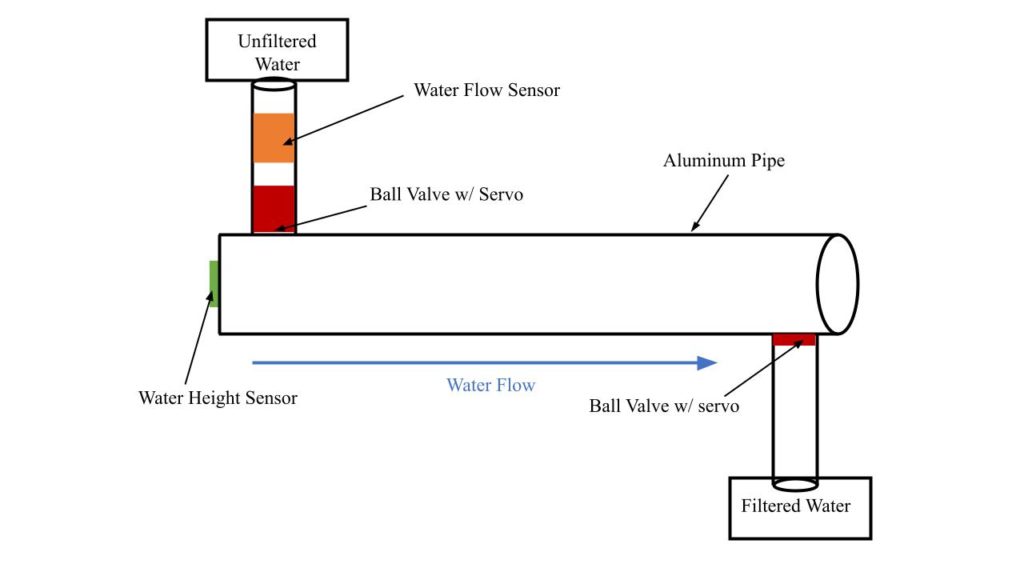
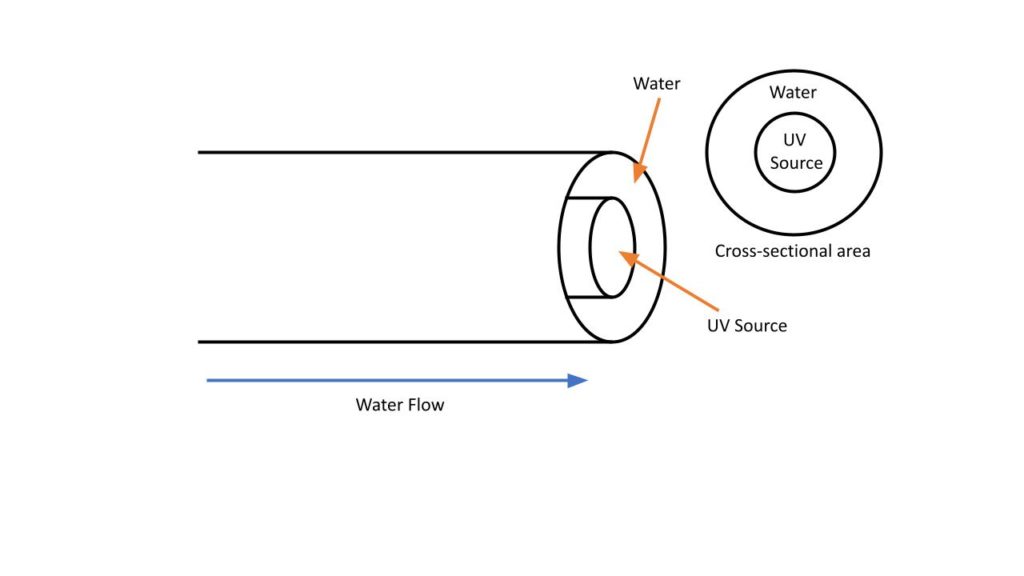
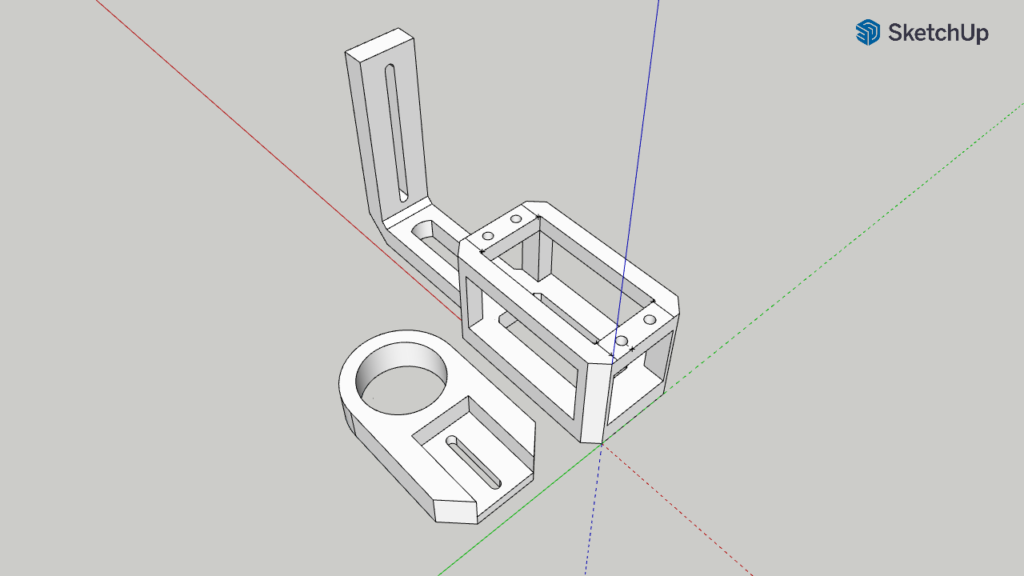
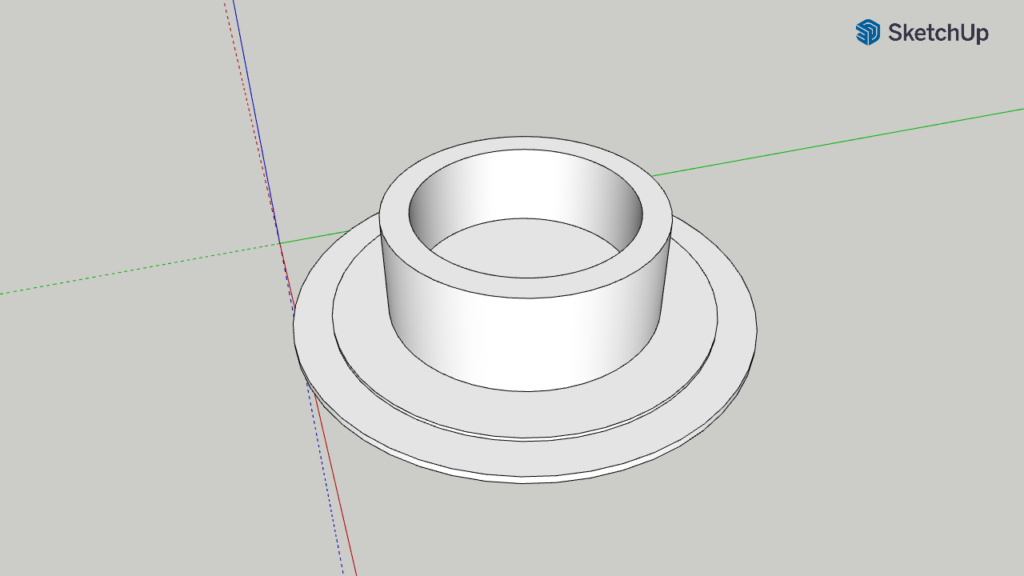
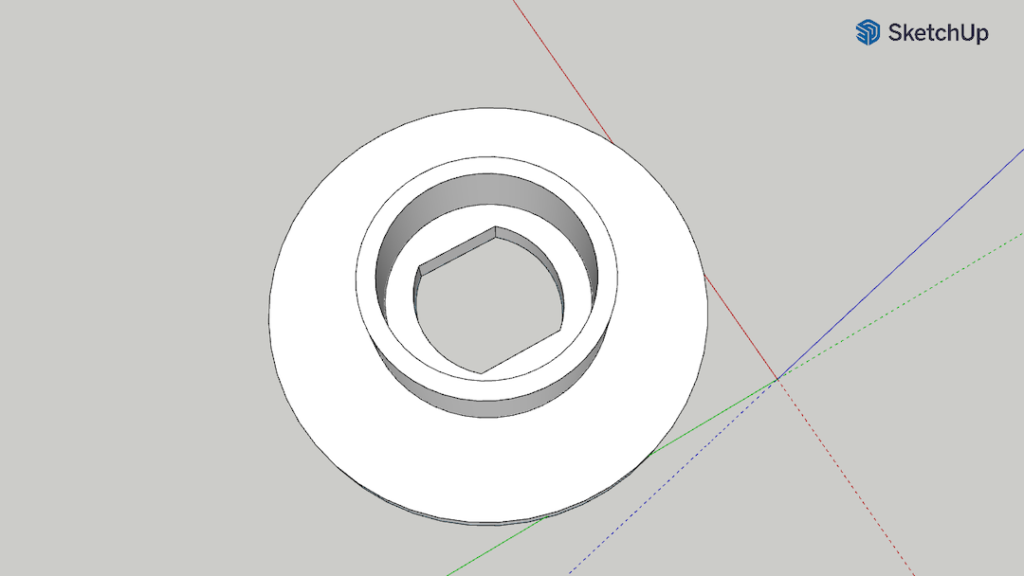


Software Implementation
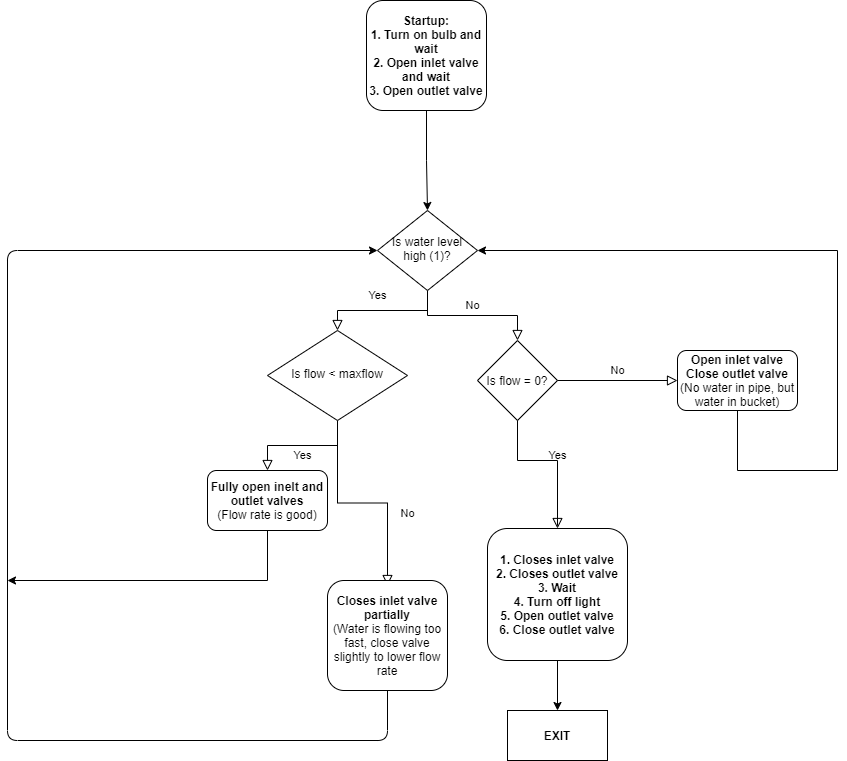
According to the specification of this UV-C bulb, the maximum allowed flow, to meet the required 40 (mW*sec/cm2) dosage intensity, was 150 gallons per hour (GPH). Since the water flow rate sensor used liters/second as unit, this equated to .04 (liters/second) for maximum allowed flow at any given point through out the system. This value was crucial in calculating the irradiation time needed to ensure the water stayed in the system long enough to meet the sterilization requirements in addition to coming up with the equation that adjusted the inlet valve according to flow rate.

Demonstrations
**Note: In the above video, we see the system in operation with water, but we do not see the inlet valve adjusting as the flow rate increases because faucet does not provide such high flow rate. This was attempted with buckets acting as a reservoir placed on higher altitude, but we still could not reach the desired flow to illustrate that the valve was adjusting in accordance. Therefore, the following video was created with signal generator providing input to the water flow rate sensor to simulate higher flow rate in order to demonstrate valve adjustment according to flow.
Final Thoughts
We were successful in designing a water sterilization control system. Our system is fully automated and operates on its own using the logic shown in software implementation. While the system is responsive to changes in flow rate and adjusts accordingly we noticed leakage from the fittings – possibly Teflon tape or high pressure fittings could be used in the future to improve the system. With additional time, we would have love to collect lab data on the effectiveness of our system in destroying pathogens to improve our overall system. Nonetheless, we are delighted to have created a system that is practical with our version one working just as we hoped.
Team Members
Charles Chimera & Mazid Muhit
Advisors
Professor Jack Mottley & Professor Daniel Phinney